Optimizing production and product control through a modern factory design
Koudijs premix animal nutrition is formulated to deliver consistent performance. Customers rely on it. This predictability requires constant attention to quality throughout the production process. Particularly since each premix is tailored to the needs of the customer. The company is flexible with its blends, but not with its standards. The premix animal nutrition factory in Veghel, the Netherlands embodies this philosophy. Nic Langeveld, Manager Premix, and Arianne Schoofs, QA Manager, tell us how the factory is designed and organised so that its output delivers maximum performance consistently.
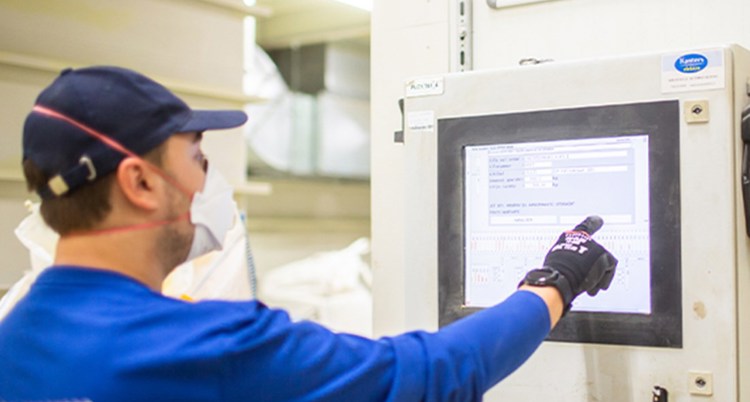
Completed in 2016, the Veghel factory is a state-of-the-art facility. "It's a modern, automated factory in terms of technology, knowledge and safety," says Nic. "We built it from scratch rather than updating an existing building which would have imposed limits." This meant that the factory could be organised to fully optimise production and product quality. About 75% of the production is sold in the Netherlands and neighbouring countries while the remaining part is manufactured for customers throughout the world. "To achieve further growth, we're very focused on the needs of customers and our commercial organisation.”
So how is the factory designed to ensure that customers get high-quality premix animal nutrition that deliver consistent, excellent performance? “Premix animal nutrition has its own standards and challenges,” Nic says. “There are five areas we need to pay close attention to: purchase and intake, tracking and tracing, accuracy of dosing, cross-contamination and homogeneity.” Producing stable, effective premixes is about more than just dosing and mixing, it involves several other disciplines as well. “We involve everyone: sourcing, formulation, mixing, production and product management,” Nic expands. “This collaborative way of working is unique. It allows us to produce extremely reliable products.”
Nothing left to chance with ingredient intake
Purchase and intake of ingredients is a main focus point and incoming materials undergo stringent checks. “The quality of our end product is strongly determined by the quality of our ingredients, so 90% of QA is devoted to intake,” says Arianne. When ingredients enter the factory they’re not just checked for quality, the QA team makes absolutely sure it’s the ingredient ordered in the quantity required from the supplier specified. “Most ingredients are some shade of white,” Arianne continues. “So you need a fool-proof identification system. Mistakes aren’t allowed.” As a result, near infrared spectroscopy (NIR) is used to identify every batch of an ingredient in addition to a visual check. “It’s a simple system that works,” adds Nic.
100% traceability throughout production
At intake, each ingredient is given a barcode so it can be tracked and traced at every point in the production process. “Each batch of every ingredient is coded as a separate intake,” says Nic. “At any time, we can trace where it was used in production and when.” This 100% traceability is unique. “We can always look back and see what’s happened in production. It’s built into our automated system,” adds Nic. “That’s the best way to guarantee the quality of our premix animal nutrition.”
Precise dosing across a very broad range
For accurate dosing of ingredients, the factory uses an automated system of over 130 silos. Each silo has an integrated weighing system which ensures precise dosing and allows constant monitoring of ingredient levels. “We have a very wide dosing range from 50 g to 1 ton,” explains Nic. “For very small quantities, we always make a dilution to ensure we dose the material correctly and mix it homogenously.”
Minimising cross-contamination
The automated dosing system is also designed to limit cross-contamination. “Every production step carries a risk of cross-contamination,” says Nic. “To minimise it, we use a closed container system for dosing.” With this system, the containers are automatically filled from the silos, transported upwards by an elevator and then the ingredients are dropped into the mixer. Using gravity in this way is recognised as one the best ways to eliminate cross-contamination and maximise product quality. The factory also uses the latest mixers to ensure perfect homogeneity.
Regular premix animal nutrition testing
Homogeneity is the final factor that contributes to highly effective premixes. “If we have the right high-quality ingredients and perform accurate dosing along with good mixing and homogeneity, we know we’re going to have good end products,” says Arianne. Nonetheless, premix animal nutrition is regularly analysed to check correct dosage and mixing.
Safeguarding the health of factory workers
This commitment to high standards extends beyond the five focus areas. The health of factory workers is also paramount. “Dust is an issue in premix animal nutrition production and it affects our choice of ingredients,” Nic explains. “We also have strong measures to keep dust as low as possible and protect staff!.” These measures include high-end filter systems, machines to remove empty bags and continuous cleaning. Staff also wear face masks and protective clothing and undergo regular medical checks.
Recipes tailored to customer needs
What about customisation? “Every customer has their own individual composition requirements,” Nic explains. “That’s why every premix we produce is tailor-made. There are no standard products.” As a result, there are a great many recipes that specifically meet each customers goals and processes. Our product managers and R&D people often give further support and advice. “We have a lot of knowledge about how premix animal nutrition behaves in animals,” continues Nic. “In addition, we get a lot of feedback from product managers about what’s happening on farms and in the market.” This information is used to develop more effective blends so that customers get optimal, predictable results.
Sharing knowledge and experience
As a large premix and animal feed producer, we have a great deal of knowledge and experience,” says Nic. “This enables us to advise customers on the most cost-effective ingredients and recipes for their specific situation. The result is reliability in terms of composition, quality, stability and animal performance. When it comes to making premix aninmal nutrition that deliver consistent performance, we’ve got everything under control.”